포토레지스트의 코팅방법은 일반적으로 스핀코팅, 딥코팅, 롤코팅으로 구분되는데, 그 중 스핀코팅이 가장 일반적으로 사용된다. 스핀 코팅을 통해 기판 위에 포토레지스트를 적하하고, 기판을 고속으로 회전시켜 포토레지스트 필름을 얻을 수 있습니다. 그 후 핫플레이트에서 가열하면 고체막을 얻을 수 있다. 스핀코팅은 초박막(약 20nm)부터 약 100um의 후막까지 코팅하는데 적합합니다. 균일성이 좋고, 웨이퍼 사이의 막두께가 균일하며, 결함이 적은 등의 특성이 있어 코팅 성능이 높은 막을 얻을 수 있습니다.
스핀 코팅 공정
스핀 코팅 시 기판의 주 회전 속도에 따라 포토레지스트의 막 두께가 결정됩니다. 회전속도와 필름두께의 관계는 다음과 같습니다.
스핀=kTn
공식에서 Spin은 회전 속도입니다. T는 필름 두께이고; k와 n은 상수입니다.
스핀 코팅 공정에 영향을 미치는 요인
필름 두께는 주회전 속도에 따라 결정되지만 실온, 습도, 포토레지스트 점도 및 포토레지스트 종류와도 관련이 있습니다. 다양한 유형의 포토레지스트 코팅 곡선 비교가 그림 1에 나와 있습니다.
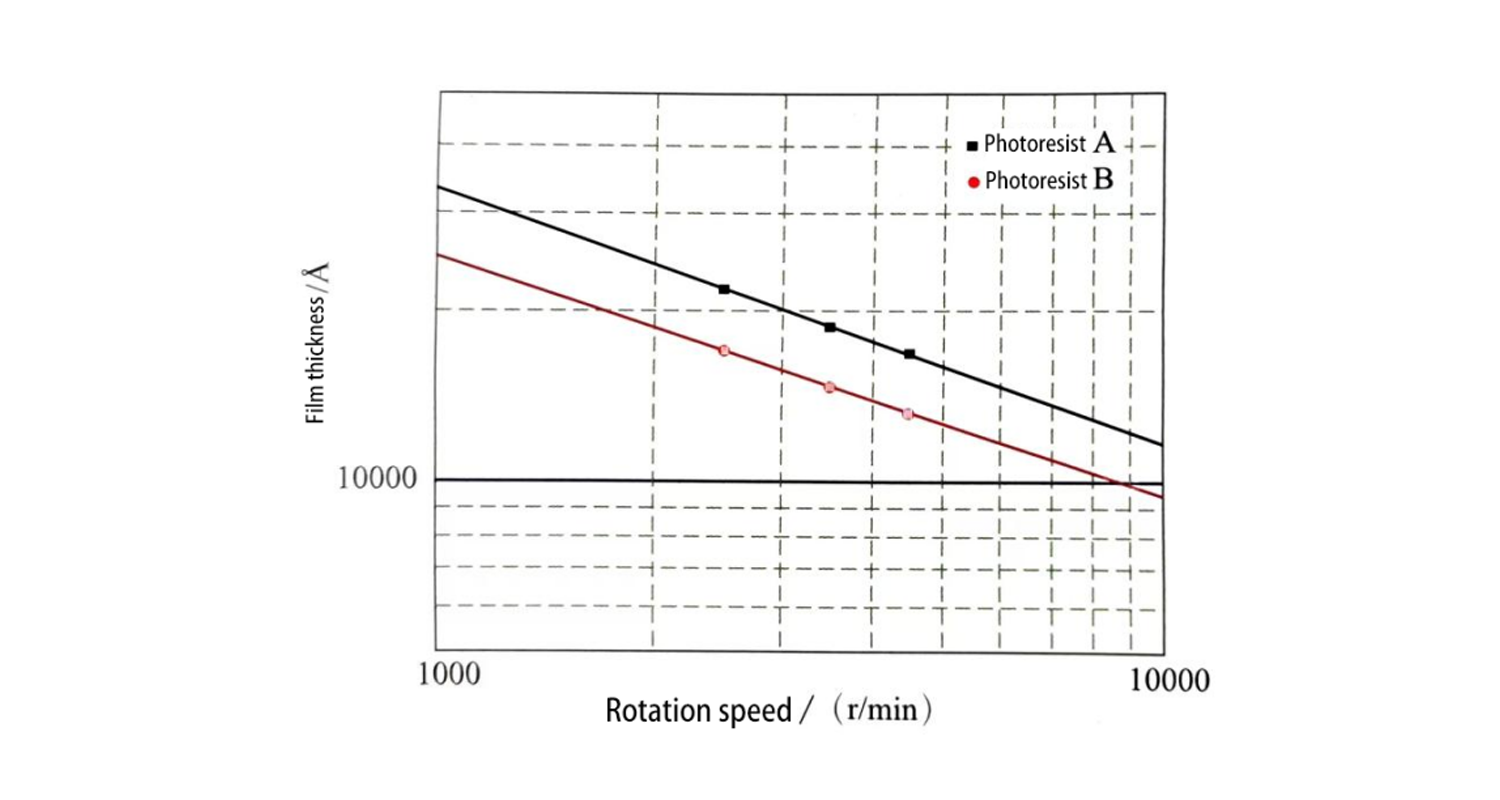
그림 1: 다양한 유형의 포토레지스트 코팅 곡선 비교
주 회전 시간의 영향
주회전 시간이 짧을수록 필름의 두께는 두꺼워집니다. 주회전 시간을 늘리면 필름이 얇아집니다. 20초를 초과하면 막 두께는 거의 변하지 않습니다. 따라서 주회전 시간은 일반적으로 20초 이상으로 선택됩니다. 주 회전 시간과 필름 두께의 관계는 그림 2에 나와 있습니다.
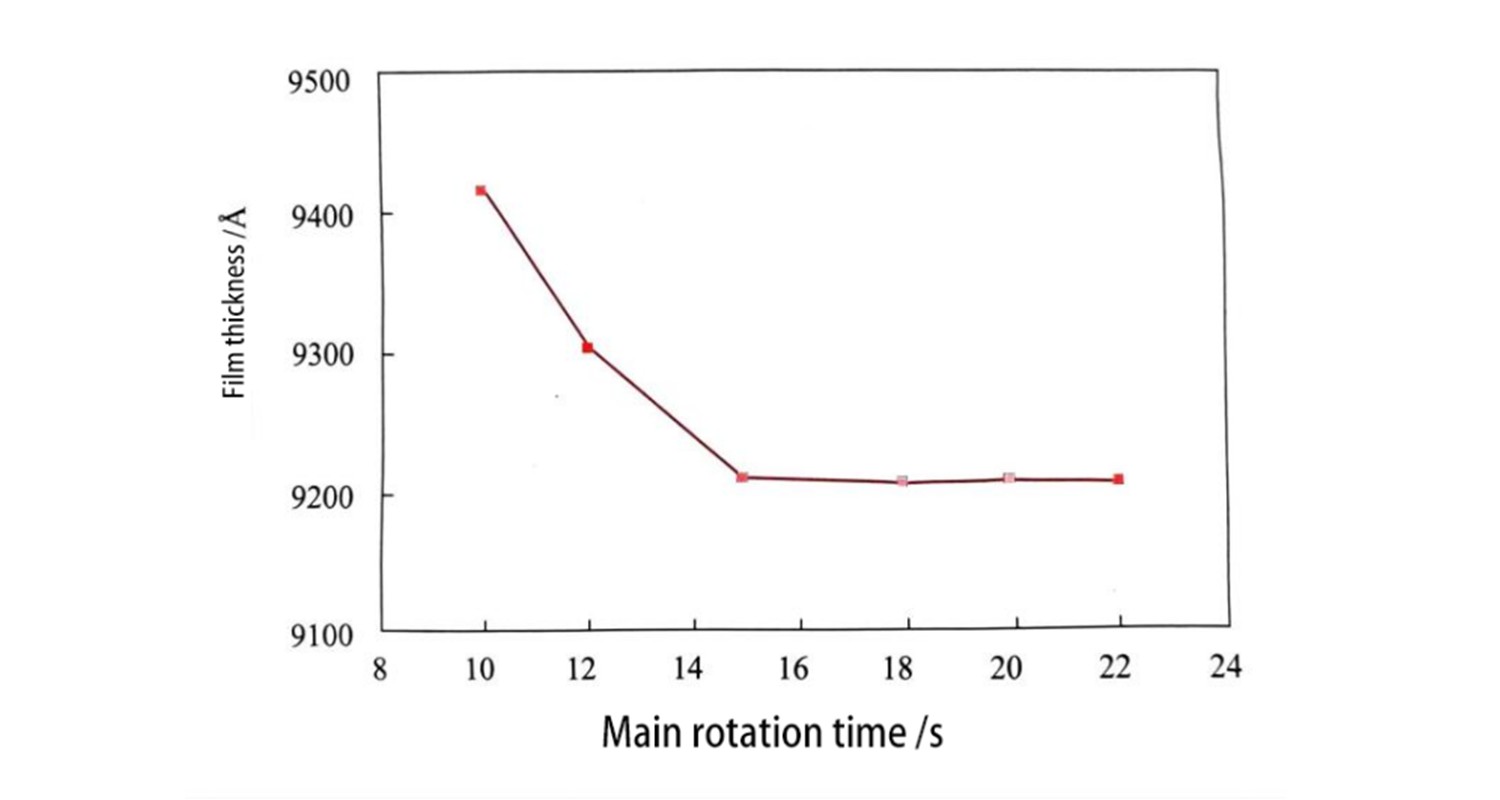
그림 2: 주회전 시간과 필름 두께의 관계
포토레지스트를 기판에 적하할 때 이후의 주 회전 속도가 동일하더라도 적하 중 기판의 회전 속도가 최종 막 두께에 영향을 미칩니다. 적하하는 동안 기판 회전 속도가 증가함에 따라 포토레지스트 필름의 두께가 증가하는데, 이는 적하 후 포토레지스트를 펼칠 때 용매 증발의 영향으로 인한 것입니다. 그림 3은 포토레지스트 적하 중 다양한 기판 회전 속도에서 필름 두께와 주 회전 속도 사이의 관계를 보여줍니다. 적하 기판의 회전 속도가 증가함에 따라 필름 두께의 변화가 더 빠르게 나타나고 주 회전 속도가 낮은 영역에서 그 차이가 더욱 분명해지는 것을 그림에서 볼 수 있습니다.
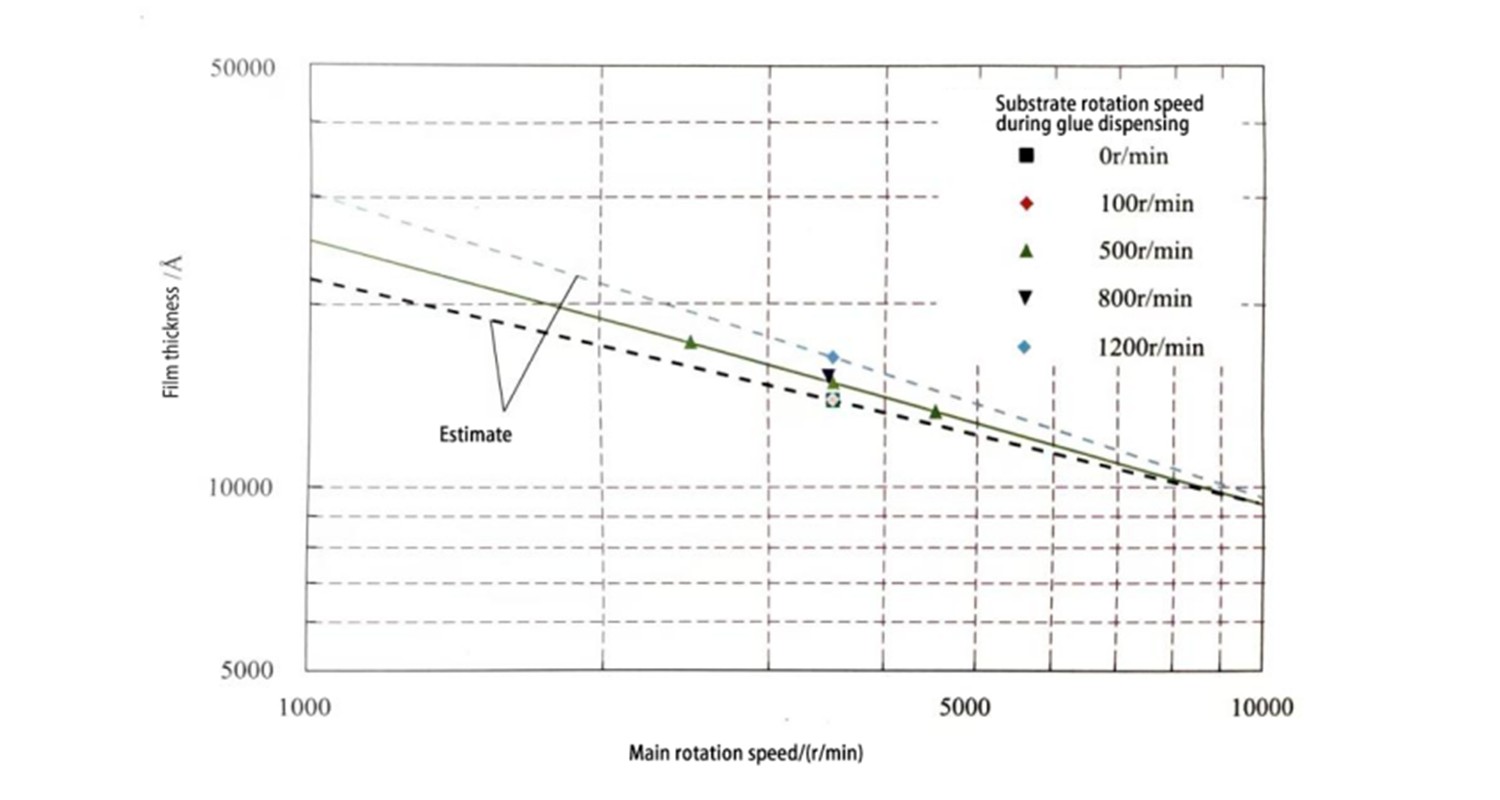
그림 3: 포토레지스트 디스펜싱 중 다양한 기판 회전 속도에서 필름 두께와 주 회전 속도 간의 관계
코팅 중 습도의 영향
습도가 낮아지면 용매의 증발이 촉진되기 때문에 필름의 두께가 두꺼워집니다. 그러나 막 두께 분포는 크게 변하지 않습니다. 그림 4는 코팅 중 습도와 필름 두께 분포 사이의 관계를 보여줍니다.
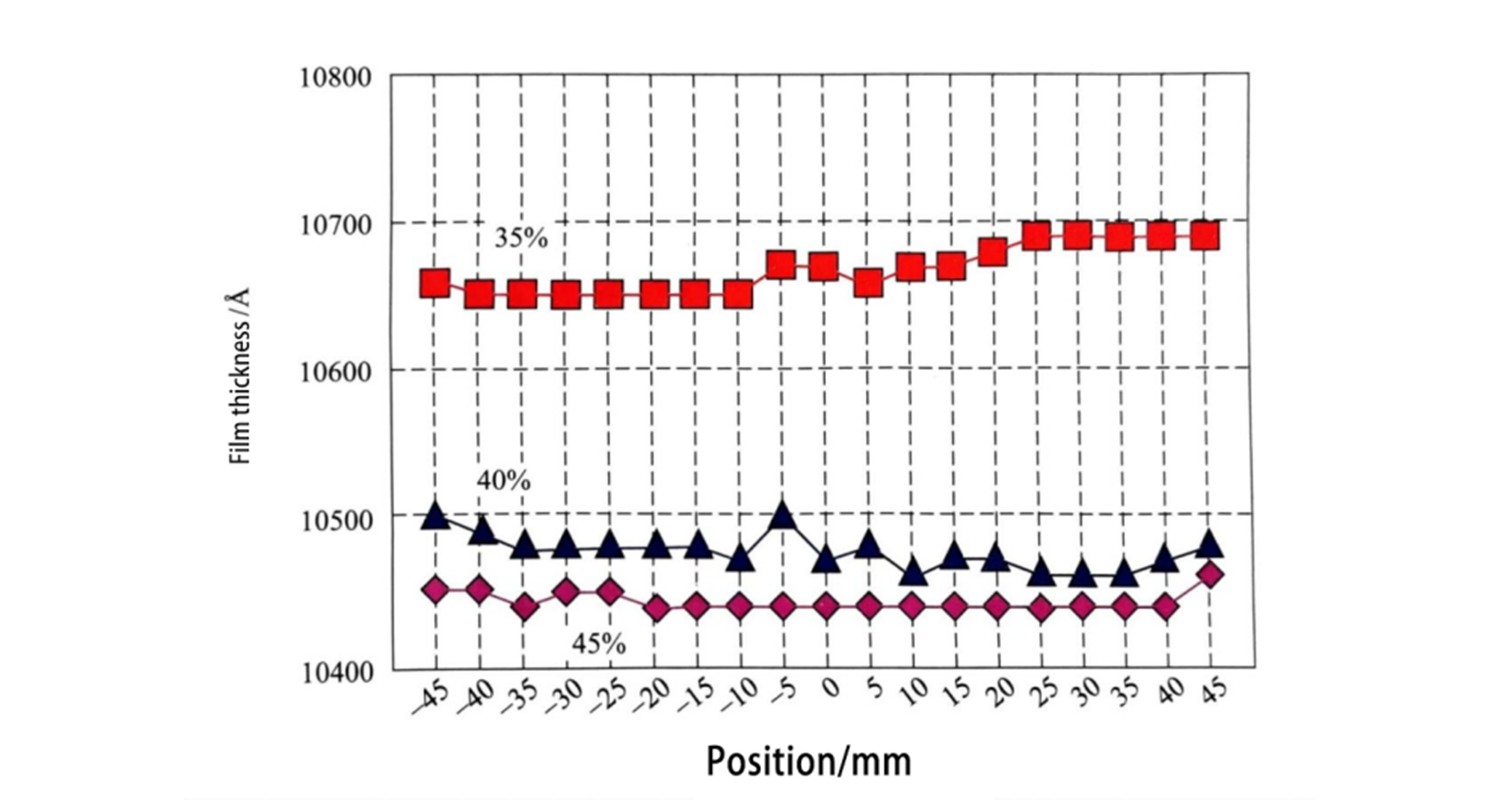
그림 4: 코팅 중 습도와 필름 두께 분포의 관계
코팅 중 온도의 영향
실내온도가 올라가면 도막두께가 증가합니다. 그림 5에서 포토레지스트 막 두께 분포가 볼록한 모양에서 오목한 모양으로 변하는 것을 볼 수 있습니다. 그림의 곡선에서도 실내 온도가 26°C, 포토레지스트 온도가 21°C일 때 가장 높은 균일성이 얻어지는 것을 알 수 있습니다.
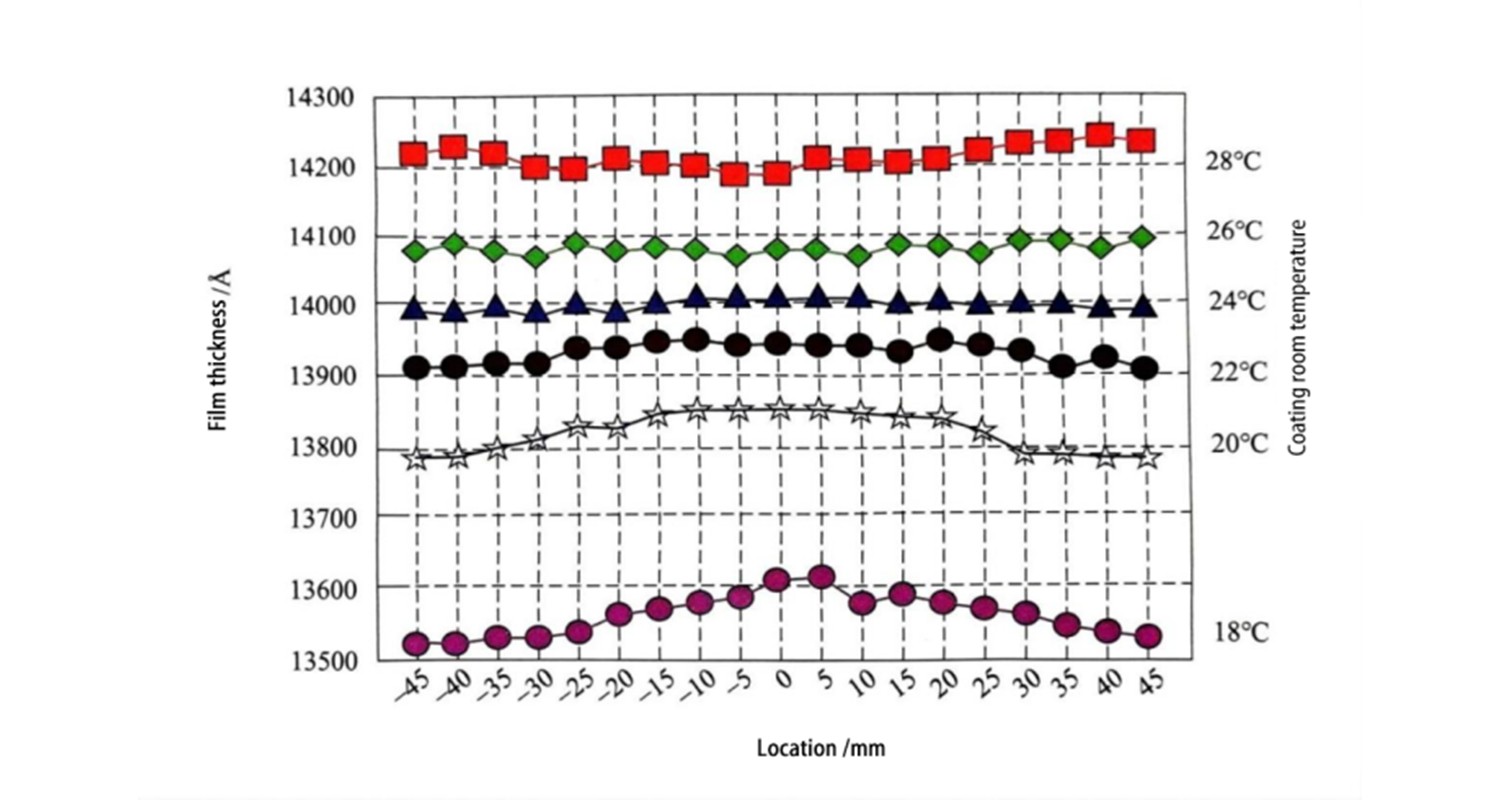
그림 5: 코팅 중 온도와 필름 두께 분포의 관계
코팅 중 배기 속도의 영향
그림 6은 배기 속도와 막 두께 분포 사이의 관계를 보여줍니다. 배기가스가 없을 경우 웨이퍼의 중심이 두꺼워지는 경향을 보인다. 배기 속도를 높이면 균일성이 향상되지만, 너무 높이면 균일성이 저하됩니다. 배기속도에 대한 최적의 값이 있음을 알 수 있다.
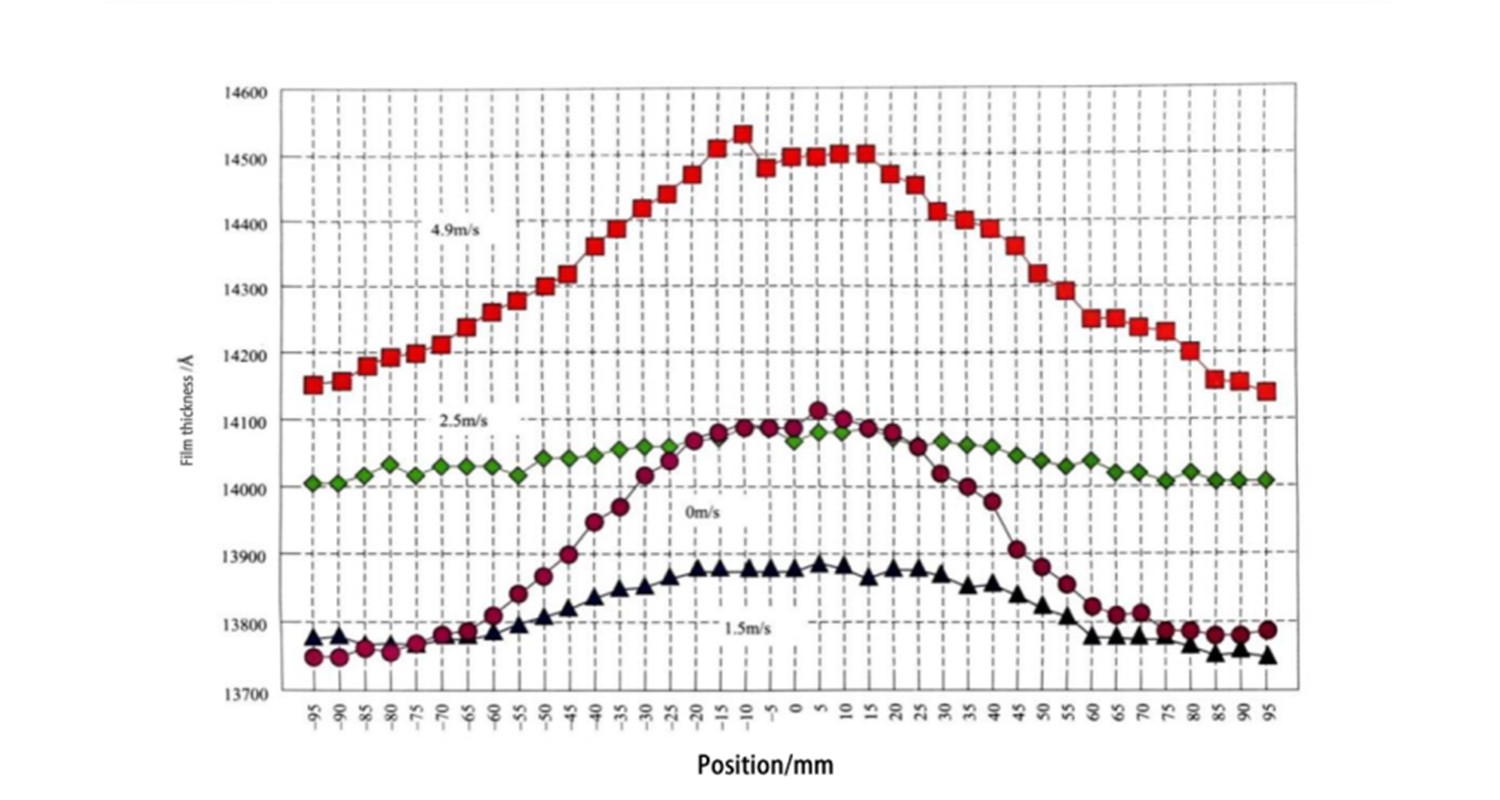
그림 6: 배기 속도와 필름 두께 분포 사이의 관계
HMDS 치료
포토레지스트의 코팅성을 높이기 위해서는 웨이퍼를 헥사메틸디실라잔(HMDS)으로 처리해야 합니다. 특히 Si 산화막 표면에 수분이 부착되면 실라놀(silanol)이 형성되어 포토레지스트 접착력이 저하된다. 수분을 제거하고 실라놀을 분해하기 위해 일반적으로 웨이퍼를 100~120°C로 가열하고 미스트 HMDS를 도입하여 화학 반응을 일으킵니다. 반응 메커니즘을 그림 7에 나타내었습니다. HMDS 처리를 통해 접촉각이 작은 친수성 표면이 접촉각이 큰 소수성 표면으로 변합니다. 웨이퍼를 가열하면 포토레지스트 접착력이 더 높아질 수 있습니다.
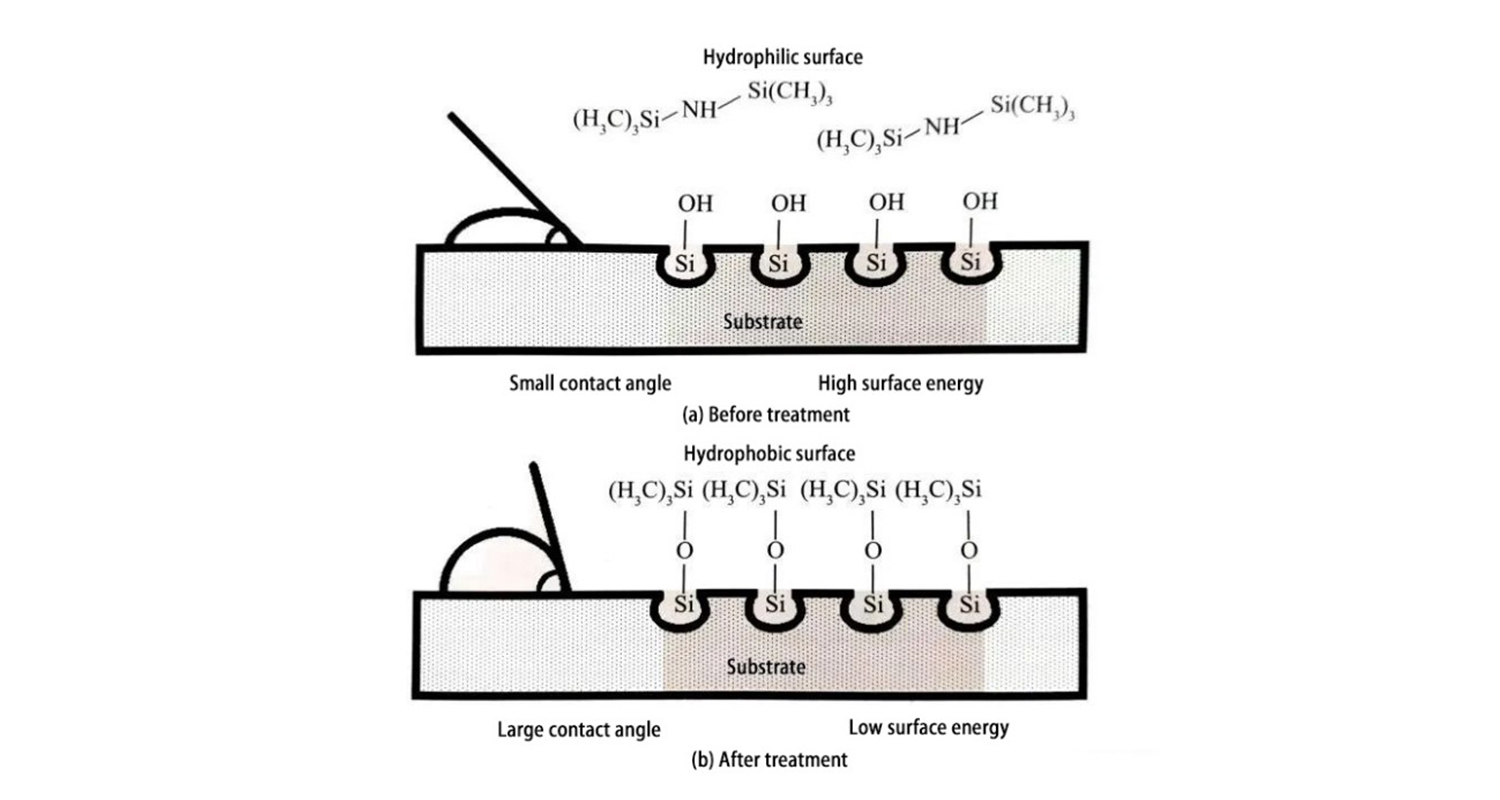
그림 7: HMDS 반응 메커니즘
HMDS 처리 효과는 접촉각을 측정하여 관찰할 수 있습니다. 그림 8은 HMDS 처리 시간과 접촉각(처리 온도 110°C) 사이의 관계를 보여줍니다. 기판은 Si이고 HMDS 처리 시간은 1분 이상이며 접촉각은 80° 이상이며 처리 효과가 안정적입니다. 그림 9는 HMDS 처리 온도와 접촉각(처리 시간 60초) 사이의 관계를 보여줍니다. 온도가 120℃를 초과하면 접촉각이 감소하여 HMDS가 열에 의해 분해되는 것을 나타냅니다. 따라서 HMDS 처리는 일반적으로 100-110℃에서 수행됩니다.
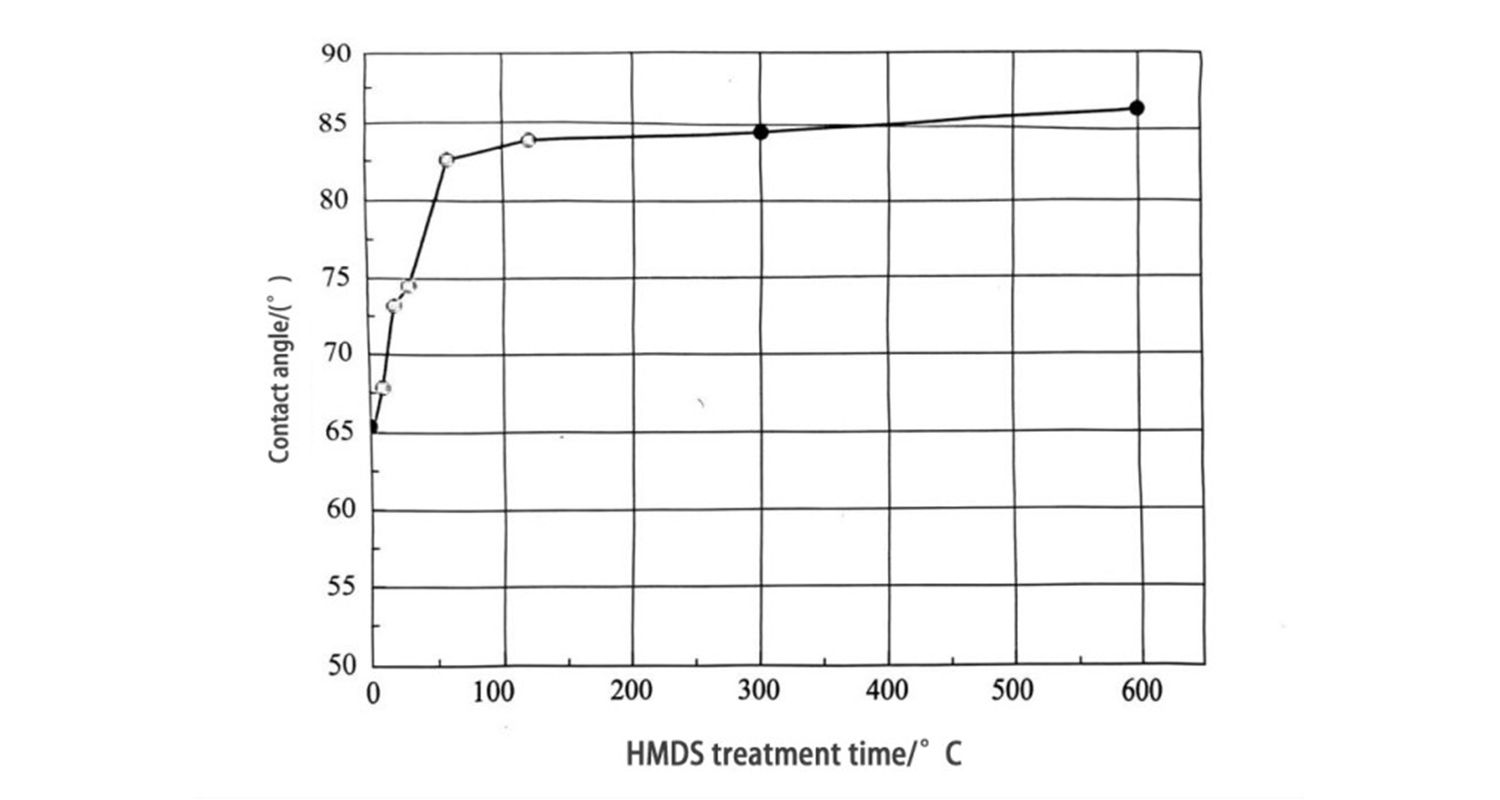
그림 8: HMDS 치료 시간 간의 관계
및 접촉각(처리온도 110℃)
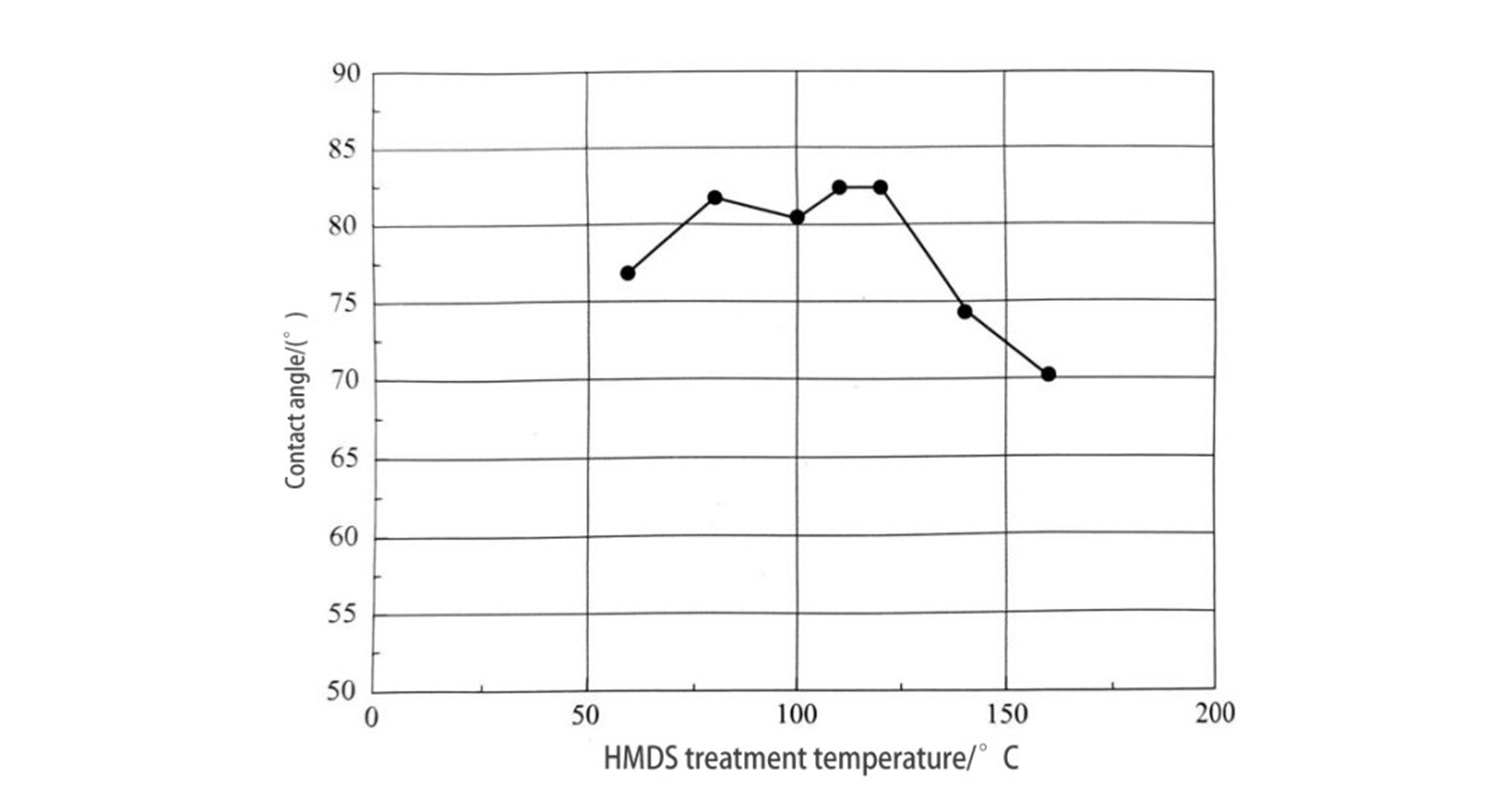
그림 9: HMDS 처리 온도와 접촉각 사이의 관계(처리 시간 60초)
산화막이 형성된 실리콘 기판에 HMDS 처리를 진행해 포토레지스트 패턴을 형성한다. 그런 다음 완충액을 첨가한 불산으로 산화막을 에칭하는데, HMDS 처리 후에도 포토레지스트 패턴이 떨어지는 것을 방지할 수 있는 것으로 나타났습니다. 그림 10은 HMDS 처리 효과를 보여줍니다(패턴 크기는 1um).
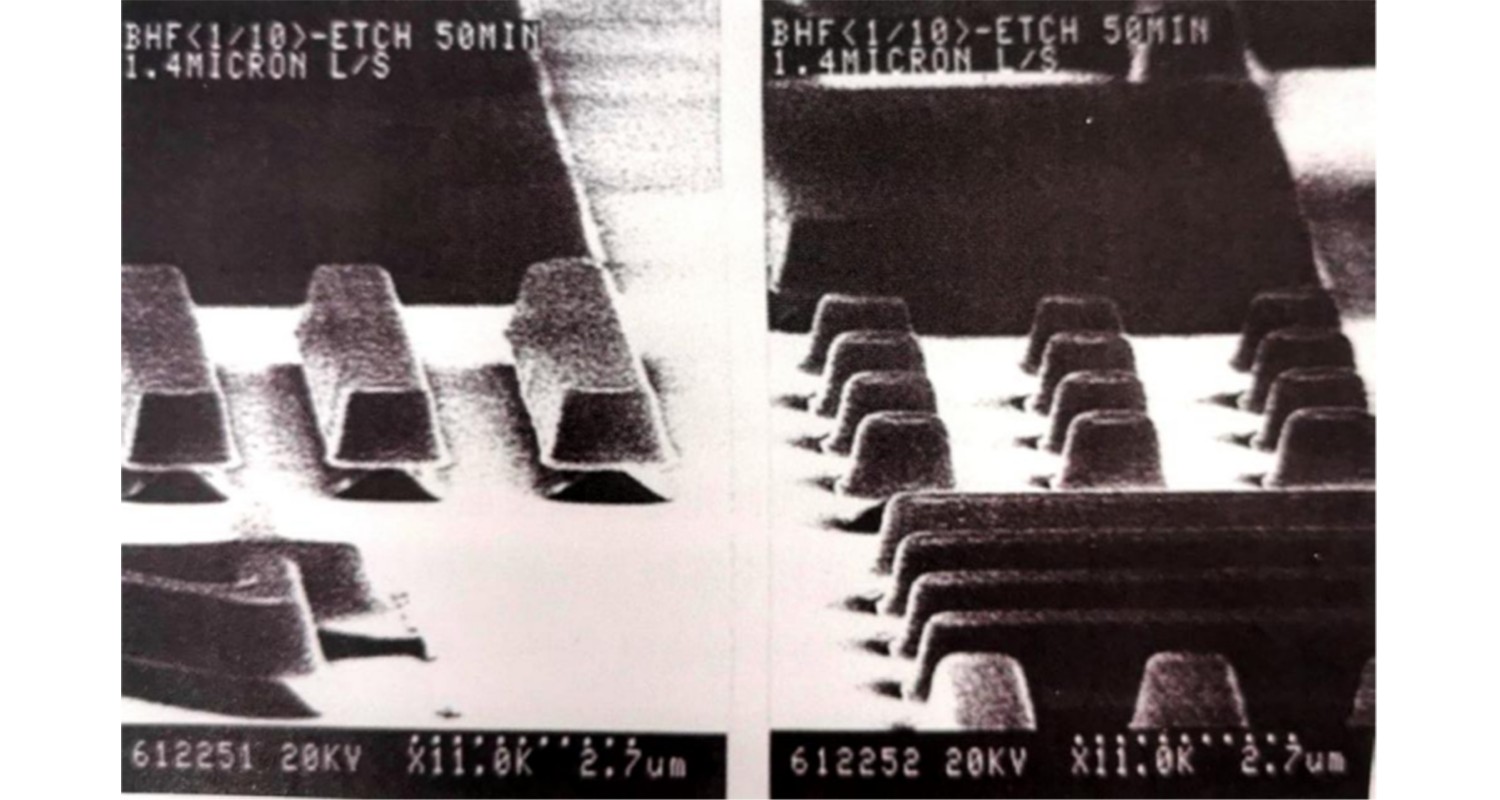
그림 10: HMDS 처리 효과(패턴 크기는 1um)
사전 굽기
동일한 회전 속도에서 프리베이킹 온도가 높을수록 필름 두께가 얇아지며, 이는 프리베이킹 온도가 높을수록 용매가 더 많이 증발하여 필름 두께가 얇아진다는 것을 의미합니다. 그림 11은 사전 베이킹 온도와 Dill의 A 매개변수 사이의 관계를 보여줍니다. A 매개변수는 감광제의 농도를 나타냅니다. 그림에서 볼 수 있듯이, 사전 베이킹 온도가 140°C 이상으로 상승하면 A 매개변수가 감소하여 이보다 높은 온도에서 감광제가 분해됨을 나타냅니다. 그림 12는 다양한 사전 베이킹 온도에서의 스펙트럼 투과율을 보여줍니다. 160°C 및 180°C에서는 300-500nm의 파장 범위에서 투과율의 증가가 관찰됩니다. 이는 감광제가 고온에서 소성 및 분해되는 것을 확인시켜준다. 사전 베이킹 온도는 빛의 특성과 감도에 따라 결정되는 최적의 값을 갖습니다.
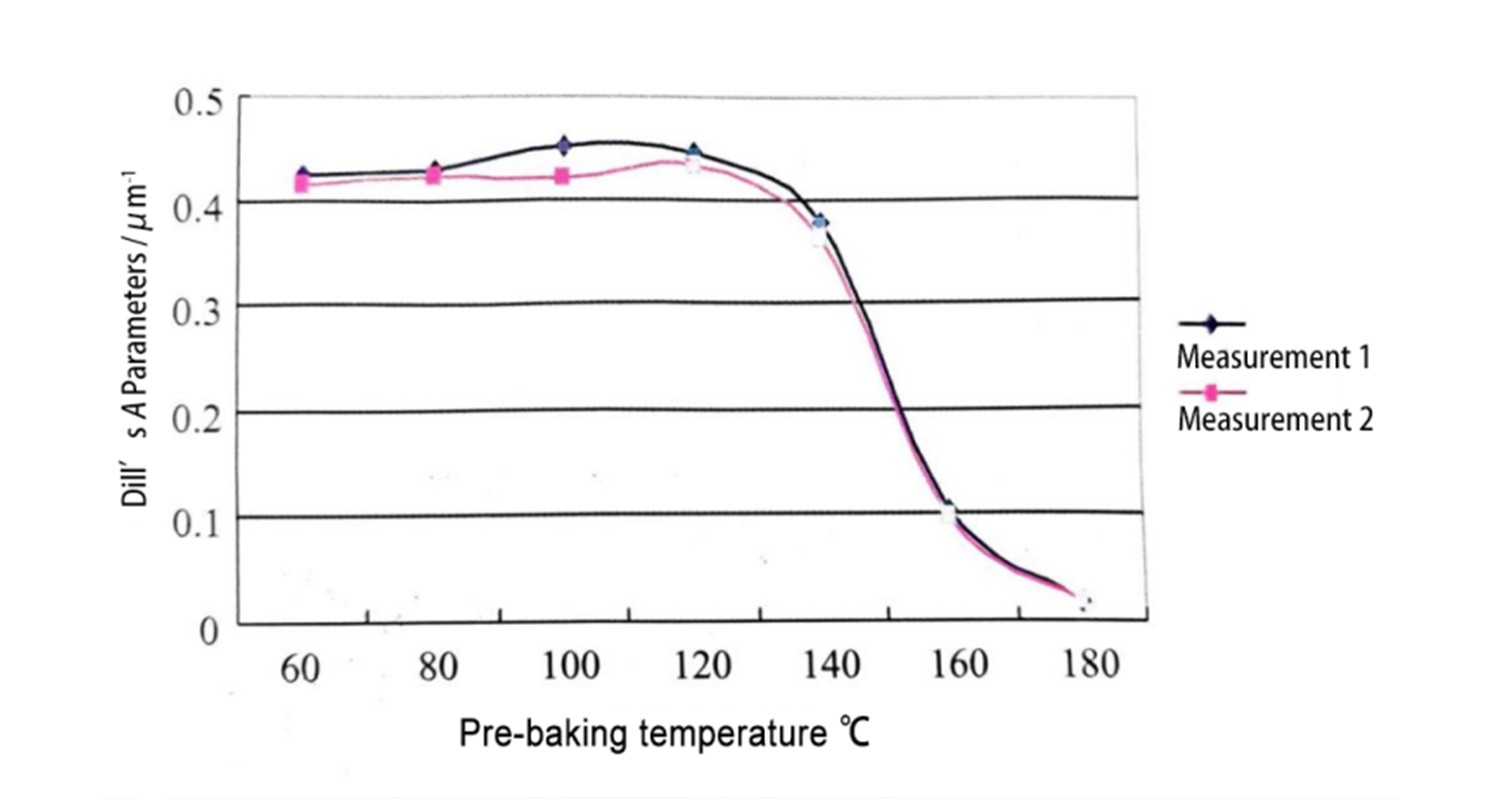
그림 11: 사전 베이킹 온도와 Dill의 A 매개변수 간의 관계
(OPR-800/2의 측정값)
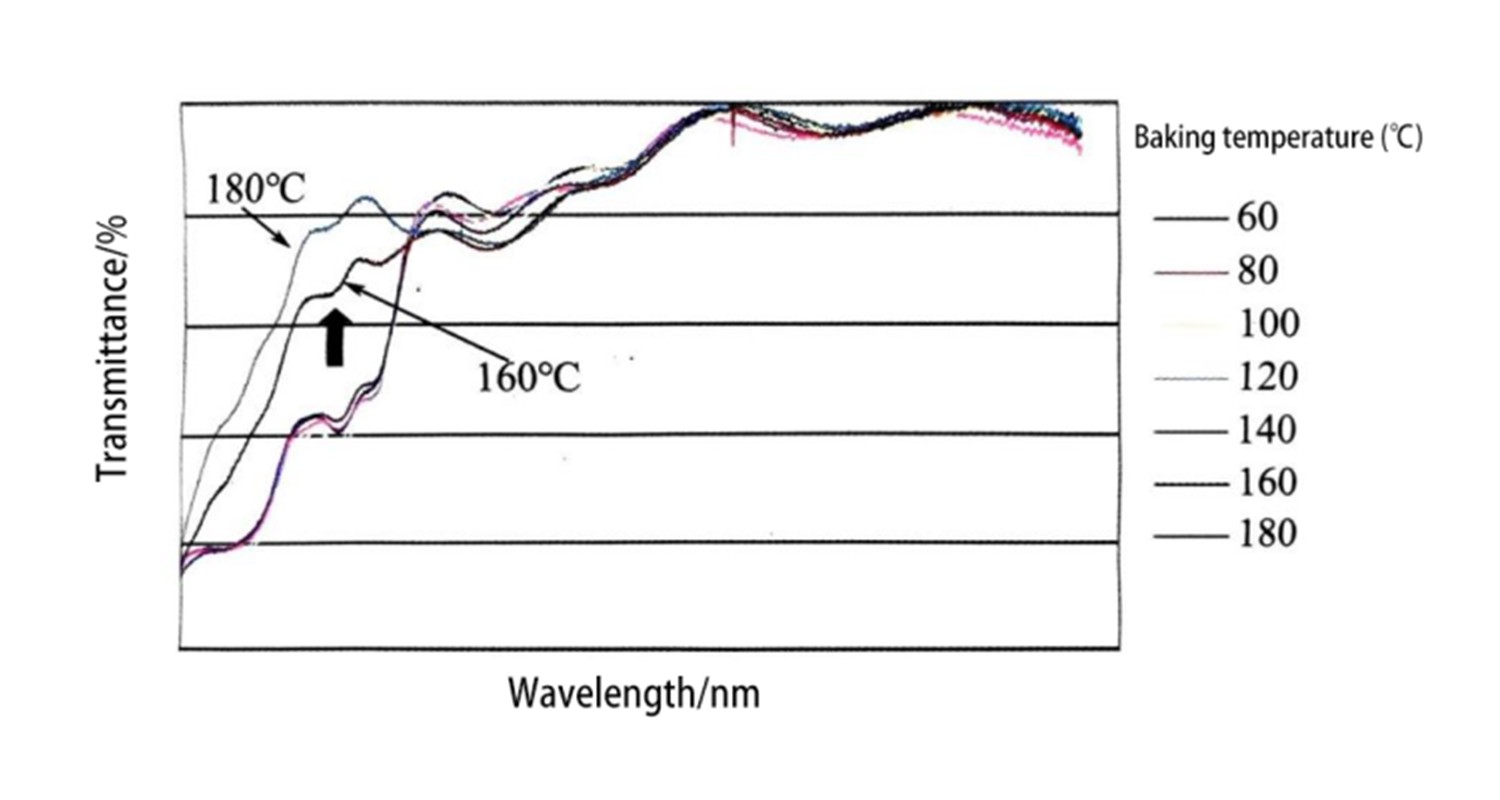
그림 12: 다양한 사전 베이킹 온도에서의 스펙트럼 투과율
(OFPR-800, 필름두께 1um)
요컨대, 스핀 코팅 방식은 막 두께의 정밀한 제어, 높은 비용 성능, 온화한 공정 조건, 간단한 조작 등 고유한 장점을 갖고 있어 오염 감소, 에너지 절약, 비용 성능 향상에 상당한 효과가 있습니다. 최근 스핀코팅에 대한 관심이 높아지고 있으며 점차 다양한 분야로 그 응용이 확산되고 있습니다.
게시 시간: 2024년 11월 27일